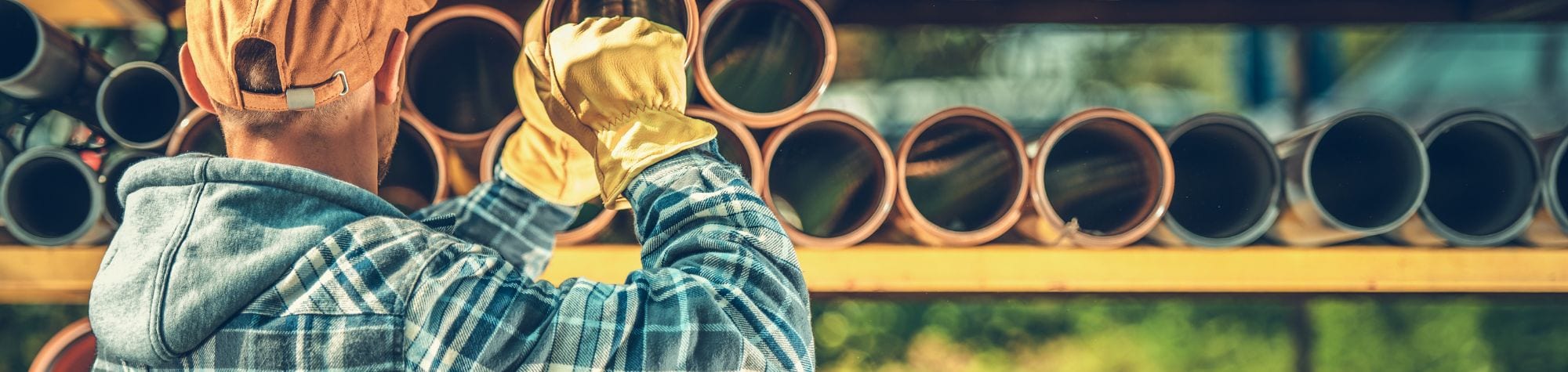
Effective supply chain management is crucial for the success of construction projects. It ensures that materials and resources are available when needed, optimizing efficiency and reducing costs. As the construction industry continues to evolve, adopting best practices in supply chain management becomes increasingly important. This article outlines these best practices, providing actionable insights for managing the complexities of construction supply chains.
Key Best Practices in Construction Supply Chain Management
1. Develop a Comprehensive Supply Chain Strategy
A well-defined supply chain strategy aligns with the overall goals of the construction project. This strategy should include detailed plans for procurement, logistics, and inventory management. According to NetSuite, having a clear strategy helps anticipate and mitigate risks, ensuring smooth project execution.
2. Utilize Advanced Technology
Integrating technology into supply chain management can significantly enhance efficiency and accuracy. Tools such as Building Information Modeling (BIM) and enterprise resource planning (ERP) systems offer real-time data and analytics, facilitating better decision-making. Buildertrend emphasizes the importance of using technology to streamline processes and improve communication among stakeholders.
3. Implement Just-in-Time (JIT) Inventory Management
Just-in-Time (JIT) inventory management minimizes waste and reduces holding costs by ordering materials only as needed. This approach requires close coordination with suppliers and accurate demand forecasting. Neuroject highlights how JIT can enhance flexibility and responsiveness in construction projects.
4. Foster Strong Supplier Relationships
Building and maintaining strong relationships with suppliers is essential for effective supply chain management. Regular communication and collaboration help ensure that suppliers understand project requirements and can deliver quality materials on time. BSI Group underscores the value of establishing trust and transparency with supply chain partners.
5. Monitor and Manage Risks
Risk management is a critical component of supply chain management. Identifying potential risks, such as supplier delays or material shortages, and developing contingency plans can help mitigate their impact. According to Buildern, proactive risk management helps maintain project timelines and budget.
6. Optimize Logistics and Transportation
Efficient logistics and transportation are vital for ensuring timely delivery of materials to construction sites. This includes selecting reliable transportation providers, optimizing delivery routes, and managing freight costs. Knowledge BSI Group recommends leveraging technology to track shipments and improve logistics coordination.
7. Implement Sustainable Practices
Sustainability is becoming increasingly important in supply chain management. Adopting sustainable practices, such as using eco-friendly materials and reducing waste, aligns with environmental regulations and corporate social responsibility goals. Buildertrend highlights the benefits of integrating sustainability into supply chain practices.
8. Leverage Data Analytics
Data analytics provides valuable insights into supply chain performance. Analyzing data on inventory levels, supplier performance, and project timelines can identify areas for improvement and drive informed decision-making. Buildertrend discusses the role of data analytics in enhancing supply chain efficiency.
Enhancing Supply Chain Management with Building Radar
Incorporating tools like Building Radar can further optimize supply chain management in construction projects. Building Radar offers an innovative solution for building product manufacturers and general contractors, enabling their sales teams to secure high-margin projects through effective specification development. By utilizing AI, Building Radar helps in the early identification of new construction projects, creating fresh sales opportunities.Building Radar’s scalable Revenue Engineering Software assists in turning projects into measurable revenue. The AI technology identifies new construction projects at the earliest opportunity, guiding sales teams to leverage their first-mover advantage. This results in more active selling time through digitized lead processes and smart process automation, ultimately leading to a higher win rate and more pipeline opportunities.Their project data spans global markets, providing early information for a competitive edge. The sales process is streamlined with easy-to-follow checklists, mobile-friendly tools, and customizable features that integrate seamlessly with downstream sales software and CRM systems. With over 45 search filters, Building Radar ensures users never miss a construction project. They also offer CRM integration with major platforms like Salesforce, HubSpot, and Microsoft Dynamics, enhancing sales efficiency through personalized customer support and data-driven insights.
Conclusion
Implementing best practices in construction supply chain management can significantly improve project efficiency, reduce costs, and enhance overall performance. By developing a comprehensive strategy, utilizing advanced technology, and fostering strong supplier relationships, construction companies can navigate the complexities of supply chain management effectively. Integrating tools like Building Radar further enhances supply chain operations, providing valuable insights and opportunities for growth.