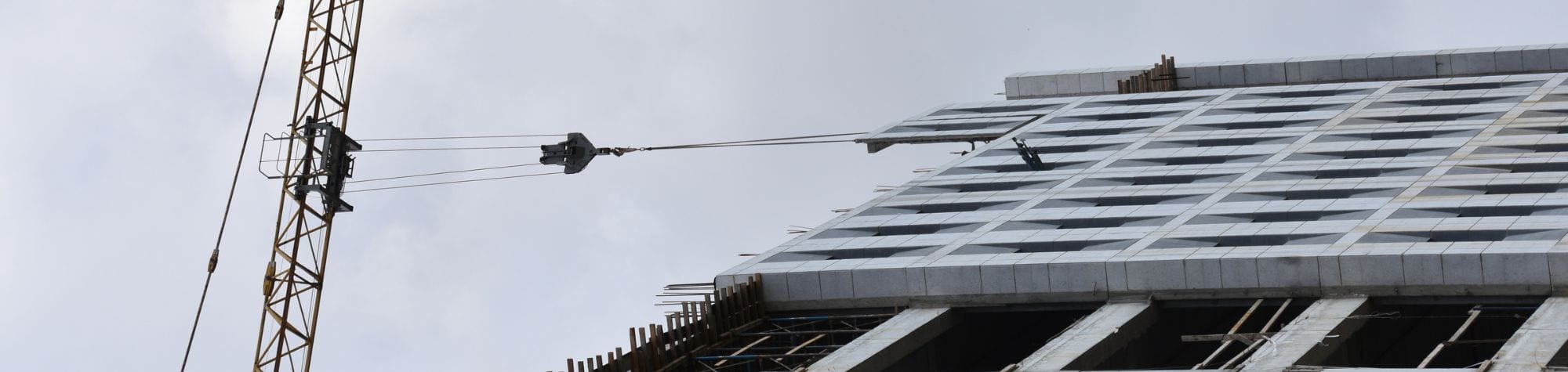
Prefabrication, often referred to as prefab, is revolutionizing the construction industry. By manufacturing building components offsite and assembling them onsite, this method offers numerous advantages over traditional construction techniques. In this article, we'll explore the benefits of prefabrication and how it can enhance construction projects.
What is Prefabrication?
Prefabrication involves producing building parts in a factory setting and then transporting them to the construction site for assembly. This process can include everything from structural components to entire rooms. Prefabrication is distinct from modular construction, which involves assembling complete sections of a building offsite.For a deeper dive into the basics of prefabrication, check out this comprehensive guide by Britannica and this insightful article by UCEM.
The Historical Context of Prefabrication
Prefabrication isn't a new concept. One of the earliest examples is the Sweet Track in England, constructed around 3,800 BCE using prefabricated timber sections. The Crystal Palace in London, built for the Great Exhibition of 1851, showcased the potential of prefabrication with its glass and iron structure.In recent years, the hospitality industry has embraced prefabrication. Marriott International, for example, has used prefab techniques to construct hotels like the Folsom Fairfield Inn & Suites in California, significantly reducing construction time and costs.
Benefits of Prefabrication in Construction
1. Time Savings
Prefabrication can significantly reduce construction time. Since components are built offsite, construction can proceed simultaneously at the factory and the job site. This parallel processing speeds up project timelines. According to Brandt, modular buildings can be constructed up to 50% faster than traditional methods.
2. Cost-Effectiveness
Building components in a controlled factory environment can reduce costs. Bulk purchasing of materials, streamlined manufacturing processes, and reduced labor costs contribute to overall savings. Prefabrication also minimizes waste, as precise manufacturing reduces material excess.
3. Enhanced Quality Control
Factory conditions allow for better quality control compared to on-site construction. Prefabricated components are built using standardized processes and materials, ensuring consistent quality. Additionally, indoor manufacturing environments are not subject to weather-related delays and damage.
4. Improved Safety
Construction sites can be hazardous, with workers exposed to various risks. Prefabrication mitigates these risks by transferring much of the work to a controlled factory setting. This reduces the time workers spend on-site, decreasing the likelihood of accidents and injuries.
5. Environmental Benefits
Prefabrication is more environmentally friendly than traditional construction methods. The controlled factory environment reduces waste, and any surplus materials can be recycled more efficiently. Additionally, the reduced need for on-site work decreases noise pollution and site disruption, benefiting the surrounding community.For further reading on the environmental impact of prefabrication, explore this article by eSUB.
6. Mitigating Labor Shortages
The construction industry often faces labor shortages. Prefabrication addresses this issue by requiring fewer on-site workers. Skilled labor in the factory can produce components efficiently, while on-site assembly requires fewer personnel, optimizing the available workforce.
7. Better Site Security
Shorter construction times and fewer on-site workers result in better site security. Prefabricated buildings go up faster, reducing the time that construction sites are vulnerable to theft and vandalism.
Current Trends in Prefabrication
Several trends are driving the adoption of prefabrication in construction:
Building Information Modeling (BIM)
BIM technology allows for detailed planning and visualization of construction projects. By integrating BIM with prefabrication, designers can optimize the use of prefabricated components, enhancing efficiency and reducing errors. Autodesk's blog provides valuable insights into how BIM and prefabrication work together.
Increased Adoption in Commercial Construction
While prefabrication has long been used in residential construction, it is now gaining traction in commercial projects. The cost and time savings, along with improved quality control, make it an attractive option for commercial buildings.
Integrating Building Radar with Prefabrication
Building Radar offers an innovative solution for building product manufacturers and general contractors, enabling their sales teams to secure high-margin projects through effective specification development. By providing tools for early identification of new construction projects using AI, Building Radar creates fresh sales opportunities.Building Radar’s scalable Revenue Engineering Software helps turn projects into measurable revenue. The AI technology identifies new construction projects at the earliest opportunity, guiding sales teams to leverage their first-mover advantage. This leads to more active selling time through digitized lead processes and smart process automation, ultimately resulting in a higher win rate and more pipeline opportunities.Their project data covers global markets, ensuring early information for a competitive edge. The sales process is streamlined with easy-to-follow checklists, mobile-friendly tools, and customizable features that integrate seamlessly with downstream sales software and CRM systems. Building Radar offers outreach tools and user-friendly templates to increase time efficiency and support best sales practices.With over 45 search filters, Building Radar ensures that users never miss a construction project. They provide seamless CRM integration with major platforms like Salesforce, HubSpot, and Microsoft Dynamics, alongside enterprise reporting to uncover sales potential in target markets. Personalized customer support is available through dedicated Customer Success Managers.Building Radar also enhances sales excellence through adaptive phone scripts, email sequences, and self-learning systems. They assist in identifying buying centers, company networks, and relevant decision-makers, continually improving the sales process with data-driven insights. Key-account tracking and discovering new companies are simplified, and comprehensive contact details are provided to support proactive sales efforts. AI-driven recommendations help customers focus on the most promising projects, saving time with automatic sequences and direct CRM integration.By incorporating Building Radar into prefabrication projects, companies can gain a competitive edge, streamline their sales processes, and ensure they never miss an opportunity.
Conclusion
Prefabrication offers numerous benefits, including time and cost savings, enhanced quality control, improved safety, and environmental advantages. As construction technology continues to evolve, prefabrication is set to become an even more integral part of the industry. By leveraging tools like Building Radar, construction firms can maximize the benefits of prefabrication and stay ahead of the competition.For more information on prefabrication and its advantages, visit these resources:
By understanding and implementing prefabrication, construction professionals can achieve greater efficiency, sustainability, and profitability in their projects.