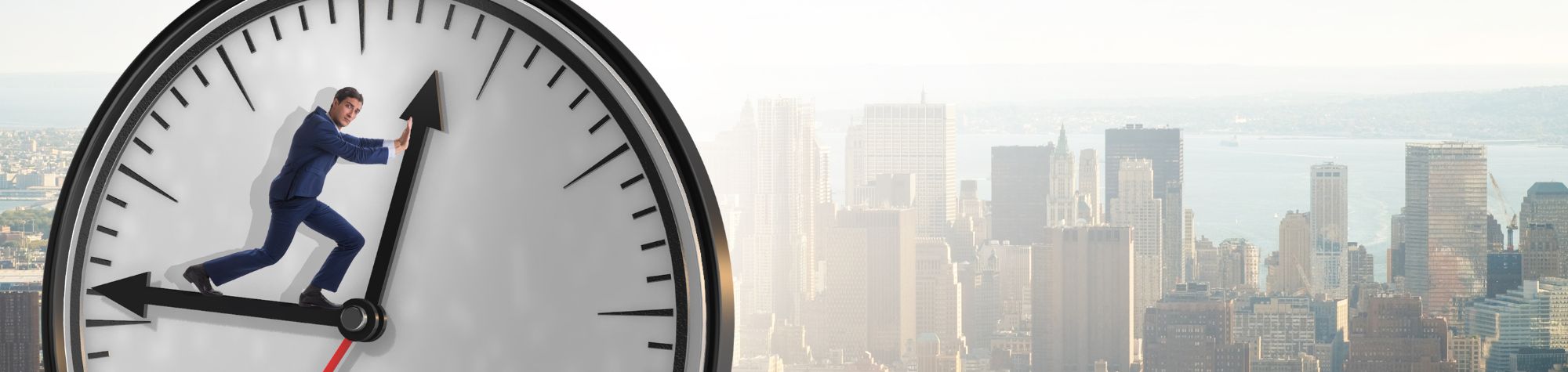
Delays in construction projects are common and costly. Whether it's a small residential build or a large infrastructure project, missed deadlines can impact budgets, client trust, and operational efficiency. Knowing what causes these delays helps project managers and teams prepare better. With tools like Building Radar offering access to over 1000 new tenders daily across 100+ countries, early planning and risk identification become achievable at scale.
Project delays usually stem from predictable patterns. By understanding these universal factors, construction firms can avoid major setbacks and deliver on time. Building Radar’s 45+ search filters help teams isolate risk-prone projects early—improving planning accuracy and increasing win rates by +310%.
1. Poor planning and scheduling
Improper planning remains one of the top causes of delay. Without realistic timelines or resource forecasts, projects quickly fall behind.
Common issues include:
- Underestimating task durations
- Lack of scheduling buffers
- Overlapping activities without coordination
- No contingency for disruptions
Using real-time tools like Building Radar allows for smarter scheduling by tracking lead times and project stages early on.
2. Inadequate site management
On-site inefficiencies can derail progress. Delays often happen due to poor site coordination and mismanagement of labor or materials.
Key contributors:
- Poor supervision
- Unorganized material storage
- Lack of access or equipment
- Slow task sequencing
Implementing site monitoring checklists and real-time reporting with Building Radar’s mobile tools can significantly reduce these issues.
3. Weather conditions
Unfavorable weather can impact project progress, especially on external or structural work. While not always avoidable, weather risks can be factored into the schedule.
Effective planning includes:
- Reviewing seasonal data
- Rescheduling high-risk tasks
- Using weather-resistant materials
- Maintaining safety in adverse conditions
Building Radar users can analyze historical trends to identify regional weather impacts early.
4. Material shortages and late deliveries
According to Sonya Ann, delays often occur due to unavailability of materials or delays in delivery. These disruptions can halt work entirely, especially when critical path items are affected. Without a clear procurement strategy and real-time supplier coordination, material issues can lead to cascading setbacks across the entire construction schedule.
Causes include:
- Supplier issues
- Global shortages
- Poor procurement planning
- Long lead times
With Building Radar, project teams can locate material producers and alternative suppliers, mitigating delay risks.
5. Labor shortages or low productivity
Skilled labor shortages or productivity dips can add weeks or months to a schedule. Many regions are experiencing talent gaps that affect timelines. This shortage is exacerbated by high industry turnover rates and a lack of vocational training programs. When teams are understaffed or poorly trained, it puts stress on timelines and quality control.
Contributing factors:
- High turnover or absenteeism
- Limited training or supervision
- Poor working conditions
- Fatigue or unsafe environments
Teams using Building Radar’s CRM integrations have improved coordination and communication, helping boost on-site productivity.
6. Design changes during construction
Change orders are unavoidable in many projects, but when design modifications happen mid-construction, they often lead to costly delays. These changes can affect not just the build schedule, but also procurement, labor coordination, and budget allocations. A reactive response to design revisions typically results in lost time and increased costs.
Delay triggers:
- Client-requested changes
- Errors in original design
- Unforeseen site conditions
- Late design approvals
By identifying project scope early using Building Radar, firms can reduce midstream disruptions and manage expectations.
7. Permitting and legal issues
Regulatory delays can bring a project to a standstill. If paperwork isn’t filed properly or approvals are slow, crews may have to halt work. Local regulations vary greatly, and misinterpreting them can result in serious consequences. Early engagement with permitting authorities and legal consultants is essential to avoid downtime.
Frequent issues:
- Incomplete documentation
- Delayed inspections
- Unclear zoning or compliance
- Legal disputes over land or contracts
Building Radar provides regional regulatory insight, supporting earlier preparation for permitting.
8. Budget overruns
Insufficient budgeting or cost overruns can stall progress when funding dries up. Without financial buffers, even small issues create big delays. Budget forecasting must factor in market volatility, especially in materials and labor. Transparent financial reporting also helps stakeholders stay aligned and committed.
Cost risks:
- Underquoted estimates
- Rising material costs
- Scope creep
- Poor cost tracking
Project teams can identify financially stable projects using Building Radar’s tender analysis, reducing financial exposure.
9. Ineffective communication
Neuroject states that breakdowns in communication are a major factor behind schedule setbacks. When teams operate in silos or lack clarity in direction, projects suffer from delays and inefficiencies. Real-time updates, standardized workflows, and open feedback channels are essential.
Root causes:
- Misaligned project expectations
- Lack of updates
- Language or cultural barriers
- Unclear change requests
CRM-backed communication via Building Radar supports faster decision-making and better information flow.
10. Equipment breakdowns
Unexpected equipment failure can bring site operations to a halt. Routine maintenance is often overlooked due to time pressure. When machines are not serviced on schedule, minor issues can escalate quickly. Equipment downtime impacts labor productivity, sequencing, and overall project flow.
Key issues:
- Outdated or overused equipment
- No backup machinery
- Untrained operators
- No preventive maintenance schedule
Tracking resource usage and downtime with Building Radar’s mobile checklists allows managers to respond quickly to equipment issues.
How Building Radar helps eliminate construction delays
Building Radar helps prevent delays by offering early visibility into upcoming projects and their risk factors. With AI-powered identification tools, teams can evaluate project complexity, forecast potential bottlenecks, and plan more effectively. This proactive approach has helped Building Radar clients gain $2.3B+ in order volume by acting earlier than their competitors.
Used by 150+ companies across 100+ countries, Building Radar simplifies lead qualification, sales enablement, and operational planning. Their platform integrates seamlessly with CRMs, provides customizable workflows, and delivers data-backed recommendations. As a result, users report +20% higher profitability and dramatically improved resource alignment throughout the construction lifecycle.
Staying ahead of the top delay risks
Understanding and preparing for universal construction delays makes project delivery more predictable and profitable. From budget gaps to weather conditions, each delay factor can be managed with the right tools and foresight. Solutions like Building Radar offer a smart, scalable way to turn insights into action—before problems occur.
Relevant Links
- Understanding Common Causes of Construction Project Delays and How to Prevent Them
- Common causes of construction delays & why a Project Timeline is crucial
- Understanding Construction Project Delays
- What Slows Down Projects and How to Avoid Delays
- Building Radar Sales Enablement Tools
- Building Radar Project Tracking
- Construction Market – UK
- Construction Market – Brazil
- CRM Integration for Project Teams
- Material Manufacturer Insights