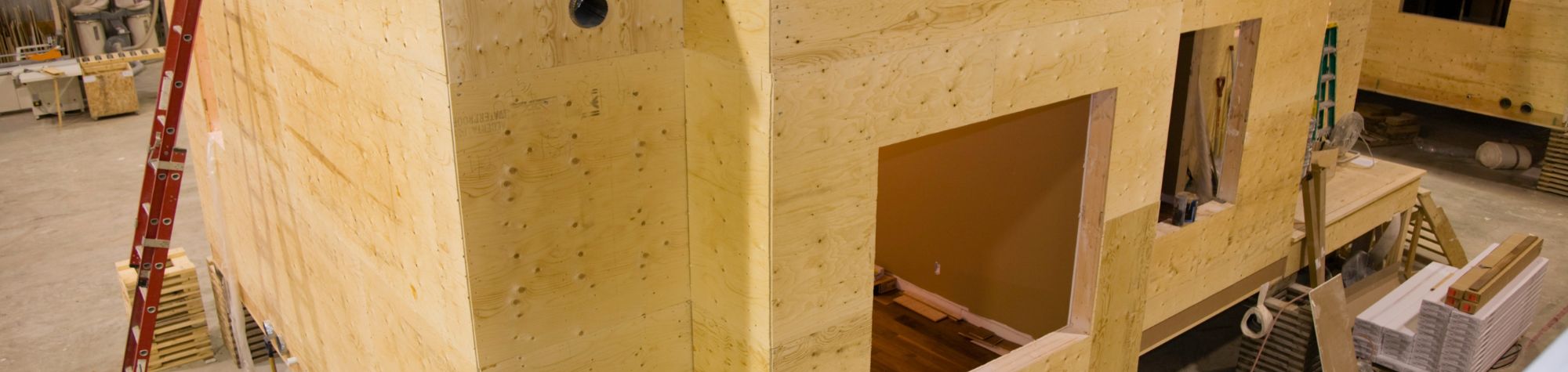
Modular construction is reshaping how buildings are designed, assembled, and delivered. Unlike traditional construction, which builds on-site from the ground up, modular construction creates building components off-site in controlled factory settings. These components—called modules—are then transported and assembled on-site, forming a complete structure. With access to early-stage project insights through platforms like Building Radar, more companies are turning to modular strategies for speed, flexibility, and quality.
According to Modular.org, modular construction uses advanced techniques and precision tools to improve building outcomes. These methods reduce material waste, shorten timelines, and enhance site safety. With Building Radar’s searchable global data, decision-makers can easily identify where modular projects are trending and align strategies to meet market demand.
How modular construction works
The process of modular construction starts with design. Using digital models like Building Information Modeling (BIM), architects plan the building down to each module’s exact specification. Once finalized, the modules are fabricated in a factory environment.
Key steps include:
- Design and planning: Completed using software for precision
- Off-site fabrication: Modules are built in a factory using prefabricated methods
- Transportation: Finished modules are delivered to the construction site
- Assembly and installation: Modules are connected on-site to form the final building
Additionally, site preparation and factory production can happen simultaneously—cutting total build time by up to 50%.
Benefits of modular construction
Modular construction offers several advantages over traditional building techniques. These benefits span cost, quality, time, and environmental performance.
Key advantages include:
- Faster build time: Parallel workflows shorten delivery
- Lower costs: Factory efficiency reduces labor and material expenses
- Improved safety: Controlled settings reduce on-site risks
- Sustainability: Less waste and better energy efficiency
- Quality control: Consistent conditions mean fewer errors
Moreover, modular methods allow for higher precision and stricter inspections. Factory construction allows for stringent quality control measures that are difficult to achieve on an open construction site. This precision reduces rework and errors, further speeding up the project timeline. Many firms now leverage platforms like Building Radar to identify modular-ready projects and fast-track bidding processes.
Challenges and limitations
Despite its benefits, modular construction also presents some limitations. These include logistical, regulatory, and design-related challenges.
Common drawbacks:
- Transportation costs: Moving large modules can be expensive
- Design constraints: May be limited by module dimensions
- Regulatory barriers: Some jurisdictions lack prefab building codes
- Perception: Viewed as less flexible than traditional builds
While modular construction is growing in popularity, it still comes with several limitations. Misconceptions about quality, site preparation needs, and the broader impact of industry labor and supply chain issues continue to challenge widespread adoption.
Modular vs. Traditional construction
Traditional construction builds a structure step-by-step at the job site. This often leads to longer timelines, weather-related disruptions, and increased costs. In contrast, modular construction speeds things up by fabricating repeatable units in parallel.
Key differences:
- Build environment: Modular is off-site; traditional is on-site
- Timeline: Modular projects are faster
- Precision: Factory settings ensure consistent results
- Flexibility: Traditional methods may offer more custom options
Modular units are adjustable and can be tailored to meet different project needs, offering both design flexibility and scalability.
Use cases of modular construction
Modular construction can be used across a wide range of sectors. It is especially valuable in industries where speed, cost, and standardization matter.
Popular applications:
- Residential homes and apartments
- Hotels and student housing
- Hospitals and clinics
- Schools and modular classrooms
- Temporary or remote site buildings
With Building Radar, companies can explore opportunities in these growing niches by filtering for modular-specific tenders using 45+ parameters.
How modular supports sustainability goals
Modular construction is an eco-friendlier alternative to traditional building. It uses fewer materials, produces less waste, and minimizes site disruption.
Environmental benefits:
- Lower CO₂ emissions from streamlined logistics
- Recycled and recyclable materials
- Less water use during construction
- Minimal noise and dust pollution
How Building Radar supports modular construction growth
With more than 150 companies leveraging its tools, Building Radar plays a key role in modular construction growth. The platform’s AI identifies early-phase modular projects worldwide—unlocking access to +1000 new tenders every day. By qualifying leads earlier and engaging sooner, users benefit from a +310% increase in win rate and enhanced forecasting capabilities.
Through automated lead discovery, customized workflows, and mobile-friendly tools, Building Radar enables sales teams to act quickly and consistently. Teams also see +20% higher profitability by influencing modular projects during early specification stages, supported by real-time insights and CRM integration across 100+ global markets.
Building smarter with modular
Modular construction is more than a trend—it’s a smarter, faster, and cleaner way to build. From homes to hospitals, the method delivers better outcomes when paired with the right tools. Using platforms like Building Radar, construction professionals can confidently adopt modular techniques and stay ahead of market shifts.
Relevant Links
- What is Modular Construction
- What is Modular Construction?
- Modular Construction: Benefits, Drawbacks, and Key Considerations
- What is a Modular Building? A Guide to Modular Construction
- Construction Market: UK
- Construction Market: Brazil
- Construction Market: China
- Building Strong Contractor Relationships
- Sales Enablement Skills
- Top Material Producers