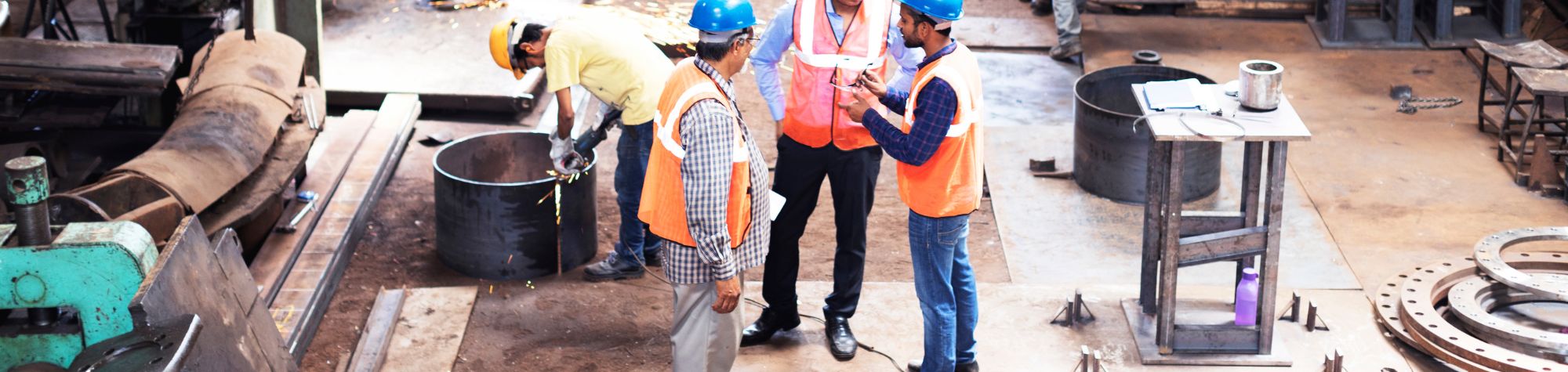
Managing a construction project often feels like piecing together an intricate puzzle. When I plan a large build, I focus on maintaining accurate records of ongoing tasks, expenses, and materials, as detailed in Indeed’s guide to construction in progress. Thorough documentation ensures that everyone—from the accountant checking the construction work in progress account to the site manager tracking daily milestones—understands how far the job has advanced. I’ve seen how referencing real-time leads, like those found in Building Radar’s construction projects database, helps me anticipate demand for subcontractors or materials. Meanwhile, comparing these leads with region-specific data, such as this Building Radar blog on the Brazilian construction market, can clarify if upcoming developments might bump up prices for concrete or steel. Another important resource is AccountingCoach’s coverage of the WIP (Work In Progress) concept, which clarifies the difference between inventory and partially finished projects. Balancing these insights with daily site logs is key to making sure you record each stage of progress consistently and accurately.
Setting the Stage with Clear Objectives
Before diving into daily logs or cost tracking, it’s crucial to outline the purpose and scope of your documentation. Deltek’s resource on construction WIP points out that when teams understand the end goals—like final building dimensions, deadlines, and budgets—they can better capture relevant data. I find that keeping an eye on external factors, such as local building codes or new tenders on Building Radar’s tenders list, helps me refine these objectives. If I see that a major competitor might break ground on a large warehouse soon, I’ll adjust my schedule or resource plans accordingly. Additionally, scanning broader trends, such as which countries excel in producing construction supplies from Building Radar’s global materials overview, reveals if I need to stockpile certain items. By defining the scope up front and linking it to real-world data, each record you create gains context, ensuring the entire project team understands the bigger picture.
Organizing Project Costs and Work In Progress Accounts
Keeping an eye on spending is a primary reason to record construction in progress. What Is Construction Work in Progress from AccountingTools emphasizes that these accounts help track incomplete projects in your financials. Rather than lumping everything into generic expense categories, you detail each stage’s costs—from excavation to electrical wiring. In my experience, referencing building cycles, such as those seen in Building Radar’s blog on the Chinese construction industry, can clarify typical cost patterns. Meanwhile, comparing these costs with local data gleaned from Building Radar’s product suite flags early warnings if materials like steel or cement face sudden price hikes. ESUB’s blog explaining CIP accounting basics underscores that when you handle these accounts carefully, you avoid surprises in the final ledger. Additionally, scanning local market demands—like what’s shown in Building Radar’s references—helps you predict if new big projects could raise labor costs mid-build. The more organized your cost entries, the simpler it is to finalize the project’s total value once it’s done.
Embracing Daily Field Reports
Field reports capture the reality of each day’s progress, from a small fix to a major milestone. AccountingCoach’s mention of daily logs in CIP workflows confirms that real-time data keeps errors from creeping into the ledger. I typically pair daily logs with external insights—like those gleaned from Building Radar’s coverage of high-margin project leads—to see if I should reallocate resources quickly. This is especially useful if an unexpected tender appears, described in Building Radar’s blog about strong contractor relationships, which might pull labor away from my current site. Another reliable source, Indeed’s CIP recordkeeping guide, suggests using mobile apps that let field supervisors photograph completed sections or note issues in real time. This tactic helps me integrate new data quickly into cost projections or scheduling software. I’ve found that short daily checklists, aligned with local building trends from Building Radar’s analysis of the UK’s construction scene, reduce guesswork for the next day’s tasks.
Using Project Management Software
Modern construction demands integrated software solutions that handle everything from scheduling to cost updates. According to Monday.com’s advice on tracking projects efficiently, a centralized platform fosters transparency among stakeholders. I personally complement these digital solutions with real-time alerts from Building Radar’s main site to see if external factors—like competitor builds or global material shortages—might affect my timeline. Another angle is gleaning tips from Twproject’s best practices for project monitoring, which highlights how automation cuts manual errors. If a surge in local development is imminent, scanning data from Building Radar’s product references shows me whether I need extra materials before prices jump. By integrating daily logs into a project management tool, I reduce the risk of duplication or oversight. And if major supply chain disruptions appear—perhaps flagged by Building Radar’s analysis of which country produces the most construction materials—my software can instantly recalculate new arrival dates or cost impacts, ensuring I always have the latest info at hand.
Digital Documentation and Cloud Storage
Cloud-based systems let you store vast amounts of construction data—blueprints, inspection photos, or cost receipts—under one roof. Deltek’s article on WIP tracking in construction warns that scattered records create confusion, especially near a build’s completion. I personally standardize file naming and version control to prevent confusion over older plan revisions. Tying in Building Radar’s tenders page ensures that if I bid on multiple new projects, I can reference past documentation to refine my cost estimates. Another approach is gleaning best practices from AccountingTools’ CIP overview, which encourages daily backups so nothing is lost if a device fails. Meanwhile, I keep track of local regulatory changes that might require updated forms, often discovered through Building Radar’s coverage of global construction markets. This streamlined system fosters a single source of truth, making compliance checks and final audits far less daunting.
Aligning Construction in Progress with Quality Standards
Quality assurance goes hand in hand with CIP documentation. ESUB’s CIP accounting guide suggests including checklists for structural integrity, materials usage, and safety compliance within each record. Whenever I see region-specific demands—like those detailed in Building Radar’s blog on how big the UK construction market is—I adapt the checklists accordingly. Cross-verifying each day’s logs with site photos ensures no quality step was overlooked. According to best practices shared in Building Radar’s blog on building strong relationships with contractors, consistent quality checks also strengthen trust among subcontractors and clients. Another useful tip is gleaning insights from accounting for CIP in the US and overseas markets, so you can standardize these checks even if you’re operating across multiple jurisdictions. Ultimately, weaving QA protocols into your CIP records means less rework and fewer disputes when the project wraps up.
Scheduling Site Inspections and Regular Audits
Frequent inspections confirm that onsite work aligns with daily logs and cost entries. Indeed’s CIP article recommends weekly or bi-weekly site visits for larger builds, where potential errors can multiply if left unchecked. I personally coordinate these audits with staff schedules in local markets, often informed by Building Radar’s product overview, to avoid clashing with busy times. Another angle is using insights from ESUB’s CIP breakdown to guide how you separate costs between labor, materials, and overhead during an inspection. Meanwhile, referencing data from Building Radar’s coverage of big construction markets in China clarifies if supply constraints might cause partial site slowdowns. These inspections let me revise daily logs or CIP accounts swiftly if I notice any discrepancy—like an undercounted set of materials or overlooked labor hours—ensuring that my records remain both current and credible.
Updating Stakeholders on Progress
Accurate CIP records benefit not just the internal accounting team, but also external stakeholders like investors, regulators, and future tenants. Deltek’s perspective on WIP in construction accounting notes that timely financial updates foster trust and reduce friction when new capital is needed. Whenever I see potential cost spikes—like a shortage of certain materials identified via Building Radar’s reference blog—I immediately alert key stakeholders. Tying in daily logs with big-picture data from AccountingTools’ CIP explanation offers an easy-to-understand snapshot of both progress and the path ahead. Another tactic is to glean communication best practices from Building Radar’s blog on key sales enablement skills, ensuring that your updates highlight essential info without drowning everyone in details. When stakeholders can see how each purchase or labor allocation fits into the broader timeline, they’re more likely to approve minor budget shifts or design modifications promptly.
Handling Deviations and Change Orders
No construction project runs exactly as planned, so CIP records must adapt to inevitable changes. What is Construction Work in Progress from ESUB underscores that changes in scope or design should be promptly reflected in both daily logs and the CIP account. I typically track these modifications in a separate ledger line, referencing cost data gleaned from Building Radar’s analysis of the biggest manufacturers of construction materials to see if the new design demands more expensive resources. Another approach is gleaning best practices from AccountingTools’ CIP insights to handle partial refunds or extra charges from suppliers. If a local competitor’s major build wraps up early—news discovered on Building Radar’s homepage—I might renegotiate certain material deals or add staff from that competitor’s pool. Documenting these moves in real time, using a single reference system, helps me keep CIP records aligned with actual progress.
Closing Out the Project
When the final inspection is done, CIP entries transition into a permanent asset account or are expensed if the build is for immediate sale. Deltek’s WIP in construction article clarifies that you typically shift costs into “Building” or “Fixed Assets” on your balance sheet. I also finalize daily logs and store them for potential audits, referencing data from Building Radar’s blog about the US, UK, or Brazilian markets to see if local regulations require extra documentation. Another recommended practice from AccountingCoach’s CIP overview is reconciling any leftover material costs or labor hours. This ensures your ledger remains accurate even if the final design differs from the original plan. Once all the numbers tally, I gather a project summary—combining cost details, site photos, daily logs, and references from Building Radar’s product library—which new leads or future clients can review. This step officially closes the loop, leaving a clear record of how each dollar was spent and how each milestone was reached.
How Building Radar Empowers CIP Documentation
From my experience, Building Radar brings a new level of clarity to how I record construction in progress. Their advanced AI scrapes global data to reveal upcoming projects before they hit traditional sources, allowing me to anticipate supply or labor bottlenecks. I explore over 45 search filters in Building Radar’s product suite to find projects that match my specs and timeline. If a massive project is about to launch nearby, I immediately adjust my CIP estimates to avoid resource shortages. Plus, direct CRM integration means I don’t have to juggle multiple platforms—everyone on my team sees the same real-time leads. This streamlined flow of information helps me keep CIP entries accurate and up to date, whether I’m tracking daily labor hours or ordering additional beams.
Building Radar also simplifies everything from lead qualification to post-build analysis. By checking their global construction project listings each morning, I see if new ventures in my region might drive up the cost of materials I rely on. If I need to pivot quickly, the checklists and digital tools embedded in the platform make it easy to revise CIP records. Meanwhile, referencing Building Radar’s tender data helps me plan future projects, verifying that each step—like formwork or finishing—reflects current market conditions. That synergy between daily logs, cost projections, and broad market intel means I never miss a beat, ensuring my CIP accounting remains solid at every stage. Ultimately, Building Radar’s intelligence translates into fewer surprises, more efficient spending, and a cohesive record of how each build transforms from concept to reality.
Final Thoughts on Organized Construction Records
A well-documented approach to recording construction in progress merges daily site observations, precise accounting principles, and real-time market intelligence. By keeping CIP accounts that reflect actual work done, referencing proven guidelines from sources like Indeed’s CIP recordkeeping tips, and integrating intelligence from Building Radar’s coverage of local leads, you ensure that each project milestone aligns with your final balance sheet. Whether you’re finalizing your daily logs with help from ESUB’s CIP accounting methods or applying cloud-based systems to unify costs, adopting these best practices pays off at every stage. Recording CIP consistently guarantees not just accurate financials, but also fosters smoother collaboration among contractors, clients, and regulatory bodies. Put it all together, and you get a transparent, proactive, and profitable construction process that stands out in an ever-competitive market.
Relevant Links
- Indeed: Construction in Progress
- ESUB: Construction in Progress Accounting
- AccountingCoach: Construction Work in Progress
- Deltek: Work in Progress in Construction
- AccountingTools: What Is Construction Work in Progress?
- Building Radar – Homepage
- Building Radar Product
- Construction Projects – Building Radar
- Tenders – Building Radar
- Reference Tools – Building Radar