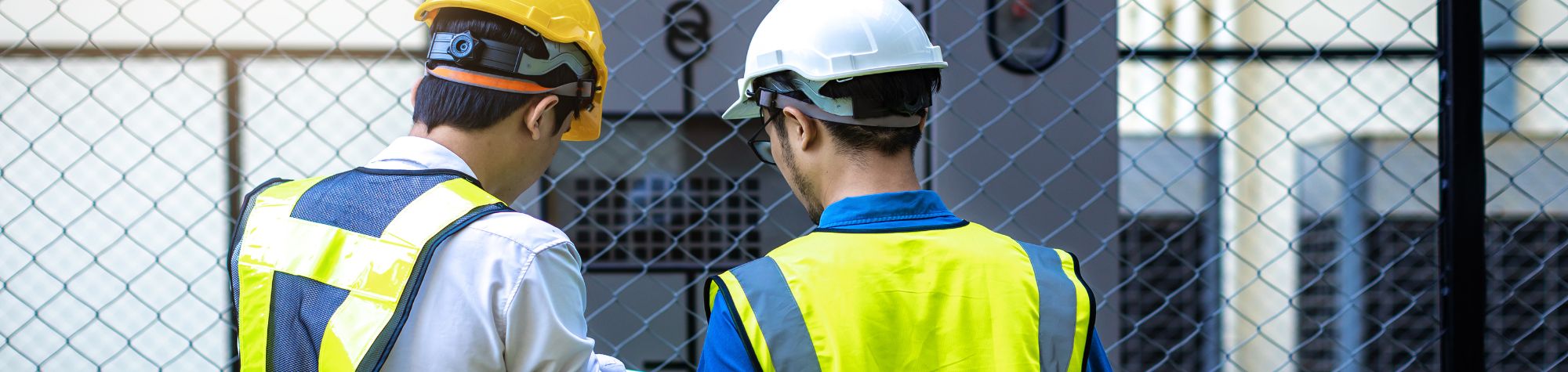
Construction projects are complex undertakings that require meticulous planning, rigorous safety standards, and constant equipment reliability. I have discovered that predictive maintenance is a forward-thinking strategy that uses advanced analytics and real-time data to forecast equipment failures and schedule proactive repairs. By using BIM systems, cloud-based management platforms, automated reporting tools, integrated CRM systems, and digital sensor networks, I have seen how predictive maintenance can revolutionize construction by preventing unexpected downtime, reducing repair costs, and enhancing overall project performance. Predictive maintenance transforms traditional reactive maintenance into a proactive process that not only increases equipment lifespan but also improves safety, ensuring that projects are completed on time and within budget—benefits that resonate with the impressive results achieved by over 150 companies using Building Radar.
I have also learned that predictive maintenance is about more than just fixing things before they break—it’s a comprehensive approach that integrates data collection, real-time analytics, and machine learning to forecast when equipment failures might occur. Utilizing automated analytics platforms, real-time dashboards, and predictive modeling tools, project managers can gain actionable insights from data generated by equipment sensors, maintenance logs, and operational parameters. This process provides the clarity needed to schedule maintenance at the most opportune times, minimize unplanned outages, and optimize resource allocation throughout the construction lifecycle—a strategy that has helped Building Radar customers achieve a $2.3B+ gain in order volume and a +310% increase in win rate.
The Fundamentals of Predictive Maintenance
Predictive maintenance in construction involves a systematic process that hinges on data collection, analysis, forecasting, and proactive intervention. I have found that understanding these fundamentals is key to implementing an effective maintenance strategy.
Data Collection and Integration
The first step is gathering data from a multitude of sources. In my experience, data is collected from BIM systems, IoT sensors installed on heavy machinery, maintenance logs, and operational software that tracks equipment usage and performance. Integrating this data into a centralized system, such as a cloud-based project management platform, allows for a unified view of all equipment performance metrics. This integration ensures that data from various sources is consistent, up-to-date, and ready for analysis, forming the backbone of any predictive maintenance program—a process that Building Radar’s digital tools support in over 100 countries.
Data Analysis and Forecasting
Once the data is collected, it needs to be analyzed to identify patterns and predict future failures. I use real-time analytics tools and interactive dashboards to monitor key performance indicators (KPIs) such as machine runtime, temperature fluctuations, vibration levels, and historical maintenance records. These tools help in identifying abnormal behavior that could indicate an impending failure. Predictive models then process this data, using machine learning algorithms to forecast potential issues. By identifying trends and anomalies, project managers like myself can schedule maintenance proactively, preventing costly downtime and extending the lifespan of critical equipment—thereby contributing to a +20% heightened profitability by influencing projects at an early stage.
Real-Time Monitoring and Alerts
Effective predictive maintenance requires continuous monitoring of equipment performance. I have implemented real-time monitoring systems that continuously gather data from sensors and transmit it to central dashboards. Automated alert systems notify maintenance teams as soon as critical thresholds are breached, enabling immediate action. This real-time feedback loop not only minimizes the risk of sudden equipment failure but also helps in planning maintenance during off-peak hours, ensuring that the workflow remains uninterrupted.
Proactive Decision Making
The ultimate goal of predictive maintenance is to move from reactive to proactive decision making. With insights generated from predictive analytics, I can forecast potential issues and decide on the optimal time to perform maintenance. This strategic approach reduces the incidence of unplanned downtime and costly emergency repairs. Automated reporting tools provide a detailed performance history, enabling informed decisions that improve overall equipment reliability and project outcomes.
Benefits of Predictive Maintenance in Construction
Adopting a predictive maintenance strategy offers numerous advantages that can transform construction project management. I have experienced several key benefits that make this approach indispensable.
Reduced Downtime and Increased Productivity
One of the most significant advantages is the reduction in unplanned downtime. By predicting when equipment is likely to fail, I can schedule maintenance during planned intervals, ensuring that projects remain on track. Real-time analytics and automated alerts allow for timely interventions, which significantly reduce the occurrence of unexpected breakdowns. This, in turn, increases overall productivity and ensures that project timelines are met without costly delays.
Cost Savings
Predictive maintenance helps in managing costs more effectively by preventing expensive emergency repairs and extending the life of equipment. I have found that scheduled maintenance, driven by data insights, is far less expensive than reactive repairs that result from equipment failures. Automated reporting and predictive analytics tools enable project managers to forecast and budget for maintenance expenses accurately, leading to significant cost savings over the project lifecycle.
Enhanced Equipment Longevity
Consistent, proactive maintenance based on predictive insights ensures that equipment is maintained in optimal condition. I have seen that equipment subjected to regular, data-informed maintenance routines experiences less wear and tear, leading to a longer operational life. Integrated maintenance schedules and data-driven performance reports help track the health of machinery, ensuring that it performs reliably throughout its lifespan.
Improved Safety and Compliance
Safety is paramount in construction, and predictive maintenance contributes significantly to a safer work environment. By using IoT sensors and real-time monitoring systems, I can detect potential hazards before they cause accidents. This proactive approach not only ensures the safety of the workforce but also helps in meeting regulatory compliance, reducing the risk of fines and legal issues. Predictive maintenance minimizes unsafe conditions by ensuring that all equipment is functioning within safe operational parameters.
Data-Driven Continuous Improvement
Predictive maintenance is an ongoing process that fosters a culture of continuous improvement. I have implemented automated reporting systems and data visualization tools to track performance over time, enabling me to refine maintenance schedules and strategies continuously. This data-driven approach ensures that the maintenance process evolves based on real-world performance data, leading to more efficient operations and improved project outcomes over time.
Better Resource Allocation and Planning
Data analytics enables better resource allocation by providing insights into equipment performance and maintenance needs. I use predictive models to forecast when equipment will require service, allowing for optimized scheduling and resource planning. This not only ensures that the right resources are available when needed but also minimizes disruptions and improves overall project efficiency. Efficient resource allocation, driven by accurate data, is critical for maximizing productivity and maintaining project schedules.
How Building Radar Enhances Data Analytics in Project Management
I am proud to share how Building Radar has played a pivotal role in enhancing our predictive maintenance strategies by providing advanced digital tools that integrate seamlessly into our project management processes. My experience with Building Radar has shown that their scalable Revenue Engineering Software identifies new construction projects at the earliest opportunity and streamlines our workflows through AI-powered analytics, automated project tracking systems, real-time reporting tools, customizable dashboards, and integrated CRM solutions. These digital solutions empower our team to collect, organize, and analyze project data effectively, enabling informed decisions that optimize maintenance schedules, reduce operational inefficiencies, and improve overall project outcomes. The impressive results achieved by Building Radar—such as a $2.3B+ gain in order volume, a +310% increase in win rate, and a +20% boost in profitability—underscore why more than 150 companies across over 100 countries trust their approach.
In our day-to-day operations, Building Radar supports our predictive maintenance initiatives by offering a comprehensive suite of integrated digital tools, including seamless CRM integration, mobile-friendly project management platforms, real-time data analytics, and automated workflow systems. My direct experience with Building Radar has enabled our team to streamline communication, enhance collaboration, and maintain rigorous oversight of every project phase. Their innovative approach to digital transformation ensures that we consistently exceed customer expectations and deliver projects with unmatched precision, safety, and efficiency.
Final Thoughts on the Advantages of a Data-Driven Approach in Project Management
After extensive research and hands-on experience, I have come to understand that the role of data analytics, particularly predictive maintenance, is transformative for construction project management. I encourage construction professionals to invest in advanced predictive analytics tools, adopt cloud-based management platforms, and implement real-time reporting systems to ensure that every maintenance decision is backed by reliable, actionable data. Focusing on continuous data collection, predictive modeling, and proactive maintenance planning allows companies to reduce downtime, optimize resource allocation, and deliver projects with superior quality and efficiency. Embracing a data-driven approach not only improves project outcomes but also provides a competitive edge that drives long-term success and customer satisfaction.
Revolutionizing project management through predictive maintenance means rethinking traditional maintenance practices and embracing innovative digital tools that transform raw data into actionable insights. With the right blend of technology, strategic planning, and continuous improvement, construction professionals can forecast risks, prevent equipment failures, and ensure that projects are executed flawlessly. I firmly believe that the future of construction lies in harnessing the power of predictive analytics to drive efficiency, enhance safety, and secure sustainable growth.
Relevant Links:
- Building Radar
- Building Radar Product
- Construction Projects
- Tenders
- Product Reference
- TechTarget: Top Predictive Analytics Tools
- Zapier: Predictive Analytics Software
- Gartner: Predictive Analytics Software Reviews
- Datarails: Top Predictive Analytics Tools
- Builtin: Predictive Analytics Tools