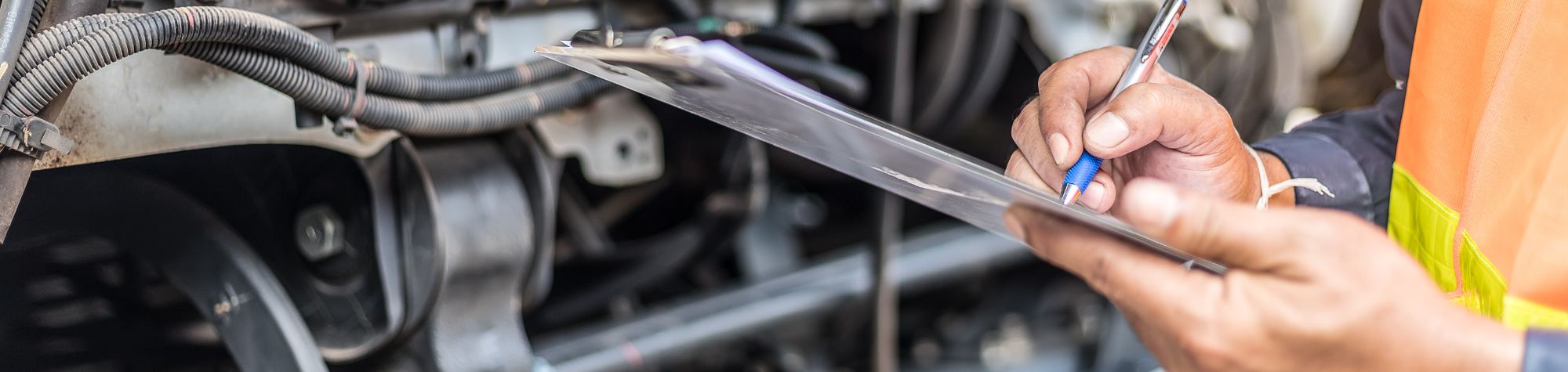
Every construction project depends on reliable equipment and seamless operations to meet strict deadlines and quality standards. I have discovered that preventive maintenance is a proactive strategy that focuses on performing regular, scheduled upkeep on equipment to prevent unexpected breakdowns, reduce costly repairs, and maintain safety on the job site. By using cloud-based project management systems, BIM software, automated reporting tools, integrated CRM systems, and digital sensor networks, I have seen how preventive maintenance transforms traditional reactive repair processes into scheduled, strategic activities that keep projects on track and under budget. This approach not only minimizes downtime but also boosts safety, ensuring that equipment operates at peak efficiency throughout the project lifecycle—a strategy trusted by over 150 companies using Building Radar, active in more than 100 countries.
I have also learned that the purpose of preventive maintenance in construction is to extend the lifespan of critical equipment and improve operational efficiency. When data from maintenance logs, IoT devices, BIM systems, and real-time monitoring tools are integrated, project managers can schedule repairs at the most opportune times, reducing the risk of unexpected failures. This data-driven strategy allows for better planning and resource allocation, ensuring that every piece of equipment is maintained in optimal condition, which in turn reduces risks and supports overall project success. In fact, Building Radar customers have experienced a +20% heightened profitability by influencing projects at an early stage, contributing to a $2.3B+ gain in order volume and a +310% increase in win rate from identification to order.
Understanding Preventive Maintenance in Construction
Preventive maintenance is a systematic approach that involves scheduled inspections, routine servicing, and proactive repairs to keep construction equipment operating efficiently. I have found that this method is vital for ensuring safety, reliability, and longevity of machinery used on job sites. It includes regular activities such as oil changes, filter replacements, calibration of instruments, and system diagnostics. By planning maintenance activities in advance through digital scheduling tools and automated checklists, managers can ensure that equipment is serviced before problems occur, reducing unexpected downtime and enhancing productivity.
A core element of preventive maintenance is data collection and analysis. I use real-time monitoring systems and automated reporting tools to gather data from various equipment sensors and maintenance logs. This data is then analyzed to identify trends and schedule maintenance activities at optimal intervals. Tools such as BIM systems and cloud-based analytics platforms help in monitoring equipment performance, ensuring that repairs and routine maintenance are carried out proactively. This data-driven approach minimizes the risk of breakdowns and ensures the reliability of construction machinery.
Key Benefits of Preventive Maintenance
The benefits of implementing preventive maintenance in construction are far-reaching and can significantly impact project outcomes:
Enhanced Equipment Reliability and Longevity
Scheduled maintenance ensures that equipment operates efficiently and lasts longer. I have experienced that regular upkeep through routine servicing and predictive monitoring helps extend the operational life of machinery. Digital sensors and automated diagnostics detect early signs of wear and tear, enabling timely repairs that prevent major failures.
Reduced Downtime and Lower Maintenance Costs
One of the most significant advantages is the reduction of unplanned downtime. By scheduling maintenance activities before equipment fails, I have observed a significant decrease in unexpected breakdowns. Automated reporting tools and real-time dashboards help identify issues early, ensuring that repairs are completed during planned downtime, thereby reducing costly emergency repairs and overall maintenance expenses.
Improved Safety and Regulatory Compliance
Preventive maintenance is critical for maintaining safety on construction sites. Regular inspections and timely repairs reduce the risk of equipment malfunctions that can lead to accidents. I have found that using maintenance management software and safety monitoring systems ensures compliance with safety standards and regulatory requirements. This not only protects workers but also reduces liability and fosters a culture of safety.
Optimized Resource Allocation and Scheduling
Efficient resource allocation is essential for project success, and preventive maintenance plays a crucial role in this aspect. By utilizing automated scheduling tools and resource management systems, I can plan maintenance activities without disrupting project timelines. This proactive approach ensures that maintenance is conducted during off-peak hours, optimizing resource usage and maintaining project continuity.
Data-Driven Decision Making
Data plays a vital role in preventive maintenance. I use real-time analytics and automated reporting to gather insights from maintenance logs and equipment performance data. These insights drive informed decision making, enabling project managers to implement proactive maintenance strategies and continuously improve processes. The use of predictive models ensures that maintenance activities are data-driven, reducing risks and enhancing overall project efficiency.
Continuous Improvement and Competitive Advantage
Adopting a preventive maintenance strategy fosters continuous improvement by providing ongoing data that can be used to refine maintenance processes. I have experienced that regular analysis of maintenance data leads to incremental improvements in efficiency, cost savings, and project performance. This culture of continuous improvement not only enhances operational performance but also provides a competitive edge in the construction industry.
How Building Radar Enhances Data Analytics in Predictive Maintenance
I am proud to share how Building Radar has significantly enhanced our predictive maintenance strategy by providing advanced digital tools that integrate seamlessly into our project management processes. My experience with Building Radar has shown that their scalable Revenue Engineering Software identifies new construction projects at the earliest opportunity and streamlines our workflows through AI-powered analytics, automated project tracking systems, real-time reporting tools, customizable dashboards, and integrated CRM solutions. These digital solutions empower our team to collect, organize, and analyze project data effectively, enabling us to schedule proactive maintenance, reduce downtime, and optimize resource allocation. The strength of this strategy is highlighted by the fact that Building Radar customers have gained over $2.3B in order volume, experienced a +310% increase in win rate from identification to order, and achieved a +20% increase in profitability—all contributing to its active use by over 150 companies in more than 100 countries.
In our day-to-day operations, Building Radar supports our data analytics and preventive maintenance initiatives by offering a comprehensive suite of integrated digital tools, including seamless CRM integration, mobile-friendly project management platforms, real-time data analytics, and automated workflow systems. My direct experience with Building Radar has enabled our team to streamline communication, improve collaboration, and maintain rigorous oversight of every project phase. Their innovative approach to digital transformation ensures that we consistently exceed customer expectations and deliver projects with unmatched precision, safety, and efficiency.
Final Insights on the Strategy for Predictive Maintenance
After extensive research and practical application, I have come to understand that the strategy for predictive maintenance is not just about reacting to equipment failures but about proactively managing them through data-driven insights and strategic planning. I encourage construction professionals to invest in advanced predictive analytics tools, adopt cloud-based management systems, and implement automated scheduling and reporting systems to ensure that maintenance is performed before issues become critical. A well-executed predictive maintenance strategy not only minimizes downtime and reduces repair costs but also enhances safety and prolongs the life of equipment, contributing to overall project success and operational excellence.
Embracing a predictive maintenance strategy means rethinking traditional repair methods and adopting a proactive, data-driven approach that integrates advanced digital tools and real-time analytics into every phase of a project. With the right blend of technology, strategic planning, and continuous improvement, construction professionals can forecast potential failures, optimize resource allocation, and ensure that projects run smoothly. I firmly believe that the future of construction maintenance lies in the power of predictive analytics to drive smarter decision making, improve performance, and secure long-term growth and customer satisfaction.
Relevant Links:
- Building Radar
- Building Radar Product
- Construction Projects
- Tenders
- Product Reference
- Techtarget: Predictive Maintenance Overview
- Fiix Software: Maintenance Strategies
- Sensemore: Strategies for Predictive Maintenance
- Artesis: Effective Predictive Maintenance
- Prometheus Group: Predictive Maintenance Considerations