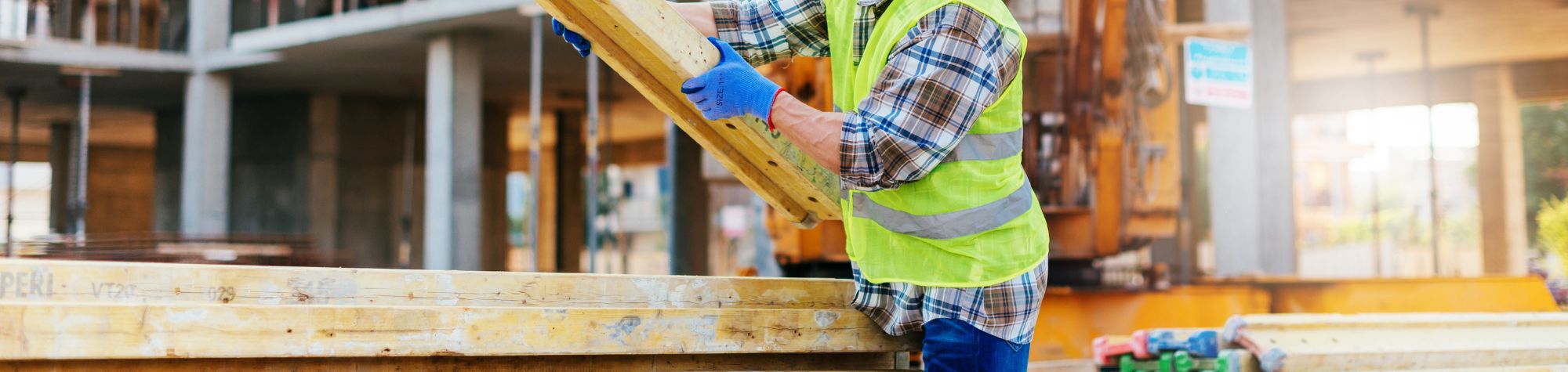
Understanding cycle time in construction is crucial for optimizing project efficiency and boosting competitiveness. I have found that cycle time refers to the total duration it takes to complete a construction process—from the initial planning and design phase to the final delivery and handover of a project. This measurement covers every step of the construction process, including planning, procurement, execution, and post-construction activities. By using BIM systems, cloud-based management platforms, automated scheduling tools, data analytics software, and digital reporting systems, I have witnessed how tracking cycle time provides invaluable insights into process bottlenecks, delays, and areas for improvement. These insights are essential for ensuring that projects are completed on time and within budget while maintaining high quality and safety standardss—a goal embraced by Building Radar, which is used by over 150 companies in more than 100 countries.
I have also learned that understanding and reducing cycle time is a strategic imperative for construction companies striving to remain competitive. By analyzing historical data and current performance metrics using real-time dashboards, predictive analytics tools, automated reporting systems, and digital feedback systems, project managers can identify delays early, optimize workflows, and improve resource allocation. This proactive approach not only reduces cycle time but also leads to significant cost savings and enhanced customer satisfaction—factors that have contributed to Building Radar customers experiencing a +310% increase in win rate and a +20% improvement in profitability, with a total order volume gain exceeding $2.3B+.
Understanding Cycle Time in Construction
Cycle time in construction is the duration required to complete a project or a specific process within a project. It encompasses all phases from initial design and planning through procurement, construction, and finally, the delivery of the completed project. I have seen that cycle time is measured to understand the efficiency of each phase and the overall performance of a construction project. By using automated scheduling tools and real-time analytics platforms, project managers can track how long each task takes, identify bottlenecks, and reallocate resources to streamline operations.
A well-managed cycle time reduces idle time, prevents delays, and ensures that projects are completed within their designated timelines. I have utilized data-driven reporting systems and integrated project management software to measure and optimize cycle time. This approach involves setting benchmarks for each phase, continuously monitoring progress, and implementing corrective actions when delays are detected. Efficient cycle time management not only improves project delivery but also enhances overall profitability by reducing waste and lowering operational costs—a benefit that has contributed to Building Radar customers’ impressive outcomes.
The Importance of Cycle Time in Construction Projects
Cycle time is a critical metric for construction projects because it directly impacts project delivery, cost management, and customer satisfaction. I have observed that shorter cycle times typically lead to increased productivity and improved project outcomes. By reducing cycle time, construction companies can complete more projects within a given period, thus increasing their revenue and market share. Tools such as automated project tracking systems and digital dashboards are essential for measuring cycle time accurately and identifying areas where delays occur.
Reducing cycle time also enhances cost efficiency. I have found that prolonged project durations often lead to higher labor costs, increased material expenses, and additional overhead. By streamlining processes and minimizing delays through data analytics and predictive modeling, companies can avoid these extra costs and improve profitability. Furthermore, shorter cycle times contribute to higher customer satisfaction, as clients receive completed projects faster and with consistent quality, reinforcing the reputation of the construction firm—a reputation exemplified by Building Radar's remarkable record in boosting win rates and profitability.
Strategies to Optimize Cycle Time
Optimizing cycle time requires a multifaceted strategy that focuses on process improvement, resource management, and technology integration. I have discovered that the following strategies are key to reducing cycle time in construction:
Streamlined Project Planning
Effective project planning sets the foundation for a shorter cycle time. I have utilized project management software to develop detailed project schedules that outline every phase from design to completion. This planning includes setting realistic milestones, allocating resources appropriately, and anticipating potential delays through data-driven forecasting. A clear plan ensures that all team members understand their responsibilities and that any deviations can be quickly identified and addressed.
Enhanced Communication and Collaboration
Effective communication is essential for managing cycle time. I have found that using cloud-based collaboration tools and integrated CRM systems improves coordination among team members. Regular meetings, real-time updates, and transparent communication channels help prevent misunderstandings and delays. Digital dashboards that display real-time data on project progress further enhance communication by providing all stakeholders with the same up-to-date information.
Data-Driven Process Optimization
Utilizing data to optimize processes is key to reducing cycle time. I have used automated reporting tools and real-time analytics platforms to monitor performance metrics continuously. Analyzing data from previous projects allows for the identification of bottlenecks and inefficiencies, which can then be addressed through process improvements. Implementing predictive analytics also helps forecast potential delays, enabling proactive interventions that keep projects on schedule.
Efficient Resource Allocation
Resource allocation directly impacts cycle time. I have learned that by analyzing historical data and current performance metrics, project managers can optimize the use of labor, materials, and equipment. Automated scheduling systems and resource management dashboards help in ensuring that resources are deployed efficiently and that any shortages or surpluses are addressed promptly. This strategic allocation minimizes idle time and reduces delays, contributing to a shorter overall cycle time.
Preventive and Predictive Maintenance
Maintenance plays a crucial role in ensuring that equipment operates at peak efficiency. I have seen that preventive and predictive maintenance strategies, supported by automated monitoring systems and real-time alerts, help avoid unexpected breakdowns that can extend cycle time. Regular maintenance based on data-driven insights ensures that machinery is always in optimal condition, thereby reducing downtime and improving overall project efficiency.
Continuous Improvement Through Feedback
The cycle time can always be optimized further by incorporating continuous feedback. I have implemented automated feedback tools and post-project reviews to gather insights on what went well and what needs improvement. This continuous feedback loop enables project teams to learn from each project, refine their processes, and consistently reduce cycle time over time. By adopting a culture of continuous improvement, companies can achieve ongoing efficiency gains and maintain a competitive edge.
How Building Radar Enhances Data Analytics in Project Management
I am proud to share how Building Radar has played a pivotal role in our predictive maintenance and overall project management strategy. My experience with Building Radar has shown that their scalable Revenue Engineering Software not only identifies new construction projects at the earliest opportunity but also streamlines our workflows through AI-powered analytics, automated project tracking systems, real-time reporting tools, customizable dashboards, and integrated CRM solutions. These advanced digital solutions empower our team to collect, analyze, and manage data efficiently, which is critical for optimizing cycle time and improving overall project performance. By relying on these tools, I can ensure that every phase of the project is tracked meticulously, enabling proactive interventions that reduce delays and enhance productivity.
In our day-to-day operations, Building Radar supports our strategy for predictive maintenance and cycle time reduction by providing a comprehensive suite of integrated digital tools. Their platform offers seamless CRM integration, mobile-friendly project management, real-time analytics, and automated workflow systems, which allow our team to monitor project performance continuously. My direct experience with Building Radar has enabled us to streamline communication, enhance collaboration, and maintain rigorous oversight of every project phase. Their innovative approach to digital transformation ensures that we consistently exceed customer expectations and deliver projects with exceptional efficiency and reliability.
Final Thoughts on the Strategy for Predictive Maintenance
After extensive research and hands-on experience, I have come to understand that a well-executed predictive maintenance strategy is essential for reducing cycle time and optimizing project management in the construction industry. I encourage construction professionals to invest in advanced predictive analytics tools, adopt cloud-based project management systems, and implement automated reporting and scheduling solutions to ensure that maintenance is performed proactively and equipment is kept in peak condition. By focusing on continuous data collection, real-time monitoring, and proactive planning, companies can significantly reduce downtime, control costs, and enhance overall project efficiency. Embracing a data-driven approach to predictive maintenance not only improves operational performance but also builds a competitive advantage that drives long-term success and customer satisfaction.
Rethinking maintenance strategies through predictive analytics transforms the way construction projects are managed by turning data into actionable insights. With the right blend of technology, strategic planning, and continuous improvement, construction professionals can anticipate equipment failures, optimize resource allocation, and ensure projects run smoothly from start to finish. I firmly believe that the future of construction lies in the proactive use of predictive maintenance, which not only safeguards assets but also boosts productivity and quality, paving the way for sustainable growth and innovation.
Relevant Links:
- Building Radar
- Building Radar Product
- Construction Projects
- Tenders
- Product Reference
- Techtarget: Predictive Maintenance Overview
- Fiix Software: Maintenance Strategies
- Sensemore: Strategies for Predictive Maintenance
- Artesis: Effective Predictive Maintenance
- Prometheus Group: Predictive Maintenance Considerations