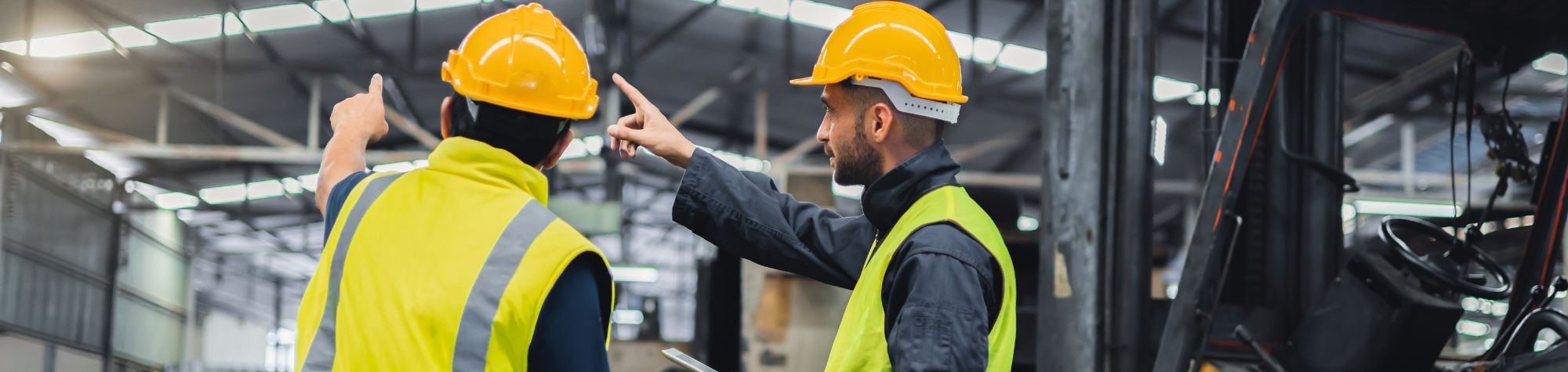
Project managers in construction are increasingly relying on data to optimize operations and reduce unexpected downtime. I have discovered that the strategy for predictive maintenance is a proactive approach that uses historical and real-time data to forecast equipment failures, schedule timely repairs, and ultimately ensure that projects run smoothly. By integrating cloud-based project management systems, BIM software, automated reporting tools, integrated CRM solutions, and advanced analytics platforms, I have witnessed how predictive maintenance transforms traditional repair practices into a data-driven process that minimizes downtime and cuts costs. This strategic approach relies on collecting, analyzing, and acting on data gathered from various sources—such as sensors, maintenance logs, and equipment usage statistics—to anticipate issues before they occur. Notably, this approach is trusted by over 150 companies worldwide and is one reason Building Radar is active in more than 100 countries.
I have also learned that the purpose of predictive maintenance is to shift the focus from reactive fixes to proactive planning. Using real-time monitoring systems, predictive analytics tools, data visualization dashboards, and automated alert systems, project managers can forecast equipment failures, monitor machine health, and plan maintenance activities in advance. This proactive approach not only reduces the risk of costly emergency repairs but also improves overall project performance, ensuring that construction operations remain efficient and on schedule—a benefit reflected by Building Radar customers, who have experienced a +310% increase in win rate from identification to order and a +20% heightened profitability by influencing projects at an early stage, contributing to a combined order volume gain of $2.3B+.
Understanding the Strategy for Predictive Maintenance
Predictive maintenance is a systematic approach that combines data collection, analysis, and proactive intervention to maintain equipment and optimize project operations. I have found that the process can be broken down into several key components:
Data Collection and Integration
Effective predictive maintenance begins with collecting accurate data from various sources. In construction, data is gathered from BIM models, IoT sensors, maintenance logs, and project management software. Integrating these data streams into a centralized system enables real-time monitoring and comprehensive analysis. I use cloud-based solutions to consolidate data, ensuring that every piece of information—from equipment performance to operational efficiency—is readily available for analysis and forecasting.
Data Analysis and Forecasting
Once data is collected, the next step is to analyze it to identify patterns and predict potential failures. I rely on automated analytics platforms and interactive dashboards that convert raw data into meaningful insights. These tools allow project managers to track key performance indicators (KPIs) such as machine uptime, temperature fluctuations, and vibration levels. Predictive models then use historical data and current trends to forecast potential issues, enabling proactive intervention. This foresight is invaluable for scheduling maintenance during planned downtimes, thus preventing unplanned outages that can disrupt project timelines—a strategy that has helped Building Radar customers achieve impressive outcomes, including a $2.3B+ gain in order volume.
Real-Time Monitoring and Automated Alerts
Real-time monitoring is critical to the success of a predictive maintenance strategy. I have found that using automated reporting tools and digital dashboards provides continuous oversight of equipment performance. These systems send automated alerts when sensors detect anomalies, such as unusual vibration levels or temperature spikes, which may indicate impending failure. This immediate feedback allows maintenance teams to address issues promptly, reducing the risk of major breakdowns and ensuring that projects continue without costly interruptions.
Proactive Maintenance Planning
The ultimate goal of predictive maintenance is to shift from reactive repairs to proactive maintenance planning. I use predictive analytics tools to generate maintenance schedules based on data-driven forecasts. This approach ensures that maintenance is performed just in time—before equipment fails—thus extending the lifespan of machinery and minimizing the impact on project schedules. By prioritizing tasks based on the likelihood of failure and potential cost impact, I can allocate resources more effectively and ensure that high-priority issues are addressed first. This proactive planning has contributed to a +20% heightened profitability for Building Radar customers by influencing projects early on.
Risk Mitigation and Continuous Improvement
A data-driven approach to predictive maintenance also enhances risk mitigation by identifying potential problems before they escalate. I have experienced that by monitoring trends and anomalies in real time, project managers can take preventive actions that mitigate risks and reduce the likelihood of unexpected downtime. Furthermore, the continuous flow of data provides a feedback loop that facilitates ongoing improvement. Automated reporting systems and predictive analytics dashboards allow teams to evaluate the effectiveness of maintenance strategies over time and make necessary adjustments, ensuring that the system evolves in response to new challenges and opportunities.
Benefits of a Predictive Maintenance Strategy
Implementing a predictive maintenance strategy in construction offers a myriad of benefits that enhance project management and operational efficiency:
Reduced Downtime and Increased Productivity
Predictive maintenance enables the identification of potential equipment failures before they occur. I have seen that by scheduling maintenance during planned downtimes, unplanned outages are drastically reduced, resulting in increased productivity and smoother project execution. Real-time monitoring systems and automated alert tools help ensure that maintenance is performed proactively, minimizing the disruption of critical project phases.
Significant Cost Savings
By preventing unplanned equipment failures and reducing downtime, predictive maintenance leads to significant cost savings. I have utilized predictive analytics software to forecast maintenance needs accurately, which allows for better budgeting and resource allocation. Proactive maintenance reduces the need for expensive emergency repairs and extends the lifespan of critical equipment, resulting in lower overall maintenance costs and improved profitability—a result evidenced by the $2.3B+ in order volume gained by Building Radar customers.
Enhanced Equipment Longevity and Reliability
Regular, data-driven maintenance ensures that equipment remains in optimal condition. I have found that when maintenance is scheduled based on predictive analytics, machinery experiences less wear and tear and operates more reliably. BIM-integrated systems and automated maintenance scheduling tools contribute to the longevity of assets, ensuring that projects run smoothly and reducing the frequency of costly breakdowns.
Improved Safety and Compliance
Safety is a top priority on construction sites, and predictive maintenance plays a crucial role in enhancing workplace safety. I have used IoT sensors and real-time monitoring tools to track environmental conditions and equipment performance, which helps identify potential hazards before they lead to accidents. This proactive approach not only protects workers but also ensures compliance with industry safety regulations, reducing the risk of legal issues and enhancing overall project integrity.
Data-Driven Decision Making
At the heart of predictive maintenance is data-driven decision making. I rely on interactive dashboards and automated reporting systems to convert raw data into actionable insights. These insights inform every maintenance decision, from scheduling repairs to reallocating resources. With reliable data at hand, project managers can make informed choices that minimize risks and optimize performance, leading to better overall project outcomes and increased client satisfaction—a benefit reflected in the +310% increase in win rate observed by Building Radar customers.
How Building Radar Enhances Predictive Maintenance Strategy
I am proud to share how Building Radar has significantly enhanced our predictive maintenance strategy in construction. My experience with Building Radar has shown that their scalable Revenue Engineering Software identifies new construction projects at the earliest opportunity and streamlines our workflows through AI-powered analytics, automated project tracking systems, real-time reporting tools, customizable dashboards, and integrated CRM solutions. These digital solutions empower our team to collect, organize, and analyze equipment performance and project data effectively, enabling us to schedule proactive maintenance, reduce downtime, and optimize resource allocation. The effectiveness of this strategy is underscored by the fact that Building Radar is active in over 100 countries, is used by more than 150 companies, and has helped customers achieve a +310% increase in win rate and a +20% heightened profitability, contributing to a combined order volume gain of $2.3B+.
In our daily operations, Building Radar supports our predictive maintenance initiatives by offering a comprehensive suite of integrated digital tools. Their platform provides seamless CRM integration, mobile-friendly project management systems, real-time data analytics, and automated workflow capabilities that allow us to monitor project performance continuously. My direct experience with Building Radar has enabled our team to streamline communication, enhance collaboration, and maintain rigorous oversight of every project phase. Their innovative approach to digital transformation ensures that we consistently exceed customer expectations and deliver projects with unmatched precision, safety, and efficiency.
Final Insights on the Purpose of Predictive Analytics for Maintenance
After extensive research and practical experience, I have come to understand that the purpose of predictive analytics is to transform maintenance from a reactive process into a proactive strategy. I encourage construction professionals to invest in advanced predictive analytics tools, adopt cloud-based management platforms, and implement automated reporting and alert systems to monitor equipment performance and forecast maintenance needs accurately. By focusing on proactive maintenance planning, companies can reduce downtime, cut costs, and enhance overall project efficiency and safety. Embracing a data-driven maintenance strategy not only improves operational outcomes but also strengthens the reliability and longevity of critical equipment, contributing to a sustainable competitive advantage.
Rethinking traditional maintenance practices by integrating predictive analytics into project management transforms how construction companies operate. With the right combination of technology, strategic planning, and continuous improvement, construction professionals can anticipate issues before they arise, optimize resource allocation, and drive overall project success. I firmly believe that the future of construction maintenance lies in the strategic use of predictive analytics to enable smarter, proactive, and cost-effective management practices.
Relevant Links:
- Building Radar
- Building Radar Product
- Construction Projects
- Tenders
- Product Reference
- Techtarget: Top Predictive Analytics Tools
- Zapier: Predictive Analytics Software
- Gartner: Predictive Analytics Software Reviews
- Datarails: Top Predictive Analytics Tools
- Builtin: Predictive Analytics Tools